Pasos efectivos para llenar el molde en la fundición con ANSYS
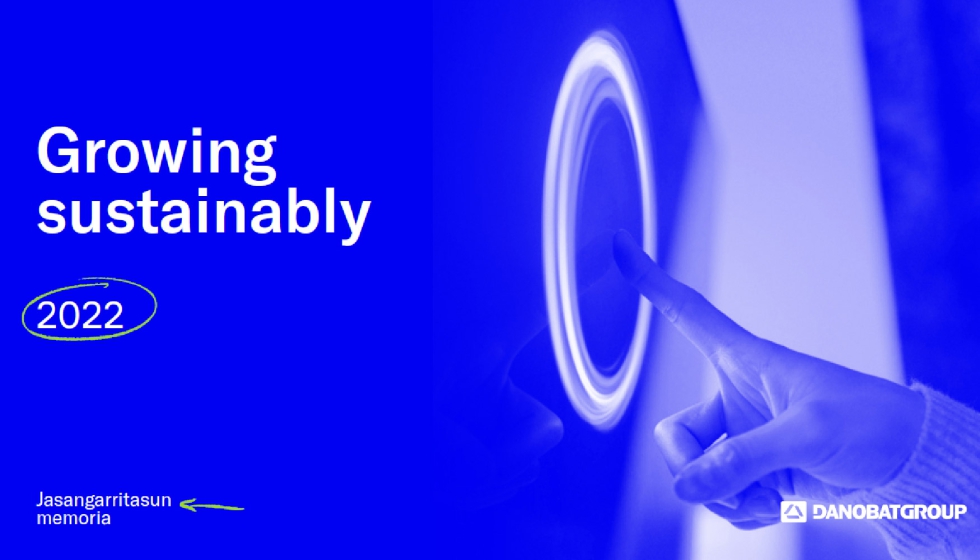
En el proceso de fundición, el llenado del molde es una etapa crítica que determina la calidad y las propiedades del producto final. El éxito de esta etapa depende de una serie de factores, como la geometría del molde, las propiedades del metal líquido y las condiciones de llenado. Se presentarán los pasos efectivos para llenar el molde en la fundición utilizando el software de simulación ANSYS.
En primer lugar, se explicará brevemente cómo funciona ANSYS y cómo puede ayudar en el proceso de fundición. Luego, se detallarán los pasos a seguir para configurar y simular el llenado del molde. Esto incluye la creación del modelo de geometría, la asignación de propiedades del material y las condiciones de contorno necesarias. Además, se discutirán las diferentes técnicas de análisis y visualización de resultados que pueden utilizarse para evaluar y optimizar el proceso de llenado. Este artículo proporcionará una guía práctica y detallada para llevar a cabo simulaciones efectivas de llenado de moldes en la fundición con ANSYS.
- Cuáles son los materiales más adecuados para utilizar en el molde en la fundición con ANSYS
- Consideraciones para el diseño del molde en la fundición con ANSYS
- Proceso de llenado del molde en la fundición con ANSYS
- Qué consideraciones se deben tener en cuenta para determinar el tamaño y la forma del molde en la fundición con ANSYS
- Cuáles son las mejores prácticas para asegurar un llenado uniforme del molde en la fundición con ANSYS
- Existen técnicas especiales para evitar defectos de llenado en el molde en la fundición con ANSYS
- Cómo se puede optimizar el tiempo de llenado del molde en la fundición con ANSYS
- Qué estrategias se pueden implementar para reducir los costos de fabricación en la fundición con ANSYS
- Cuáles son las principales dificultades o desafíos que pueden surgir al llenar el molde en la fundición con ANSYS
- Qué métodos de análisis y simulación se pueden utilizar para evaluar la calidad del llenado del molde en la fundición con ANSYS
- Es posible realizar modificaciones en el diseño del molde durante el proceso de llenado en la fundición con ANSYS
- Cuáles son los beneficios de utilizar la simulación en la fundición con ANSYS en comparación con los métodos convencionales
- Preguntas frecuentes (FAQ)
- 1. ¿Cuál es el proceso para llenar el molde en la fundición con ANSYS?
- 2. ¿Qué parámetros debo considerar al realizar la simulación de fundición con ANSYS?
- 3. ¿Cómo puedo verificar si el llenado del molde en la simulación de fundición es correcto?
- 4. ¿Qué tipos de defectos de fundición puedo prevenir con la simulación de fundición en ANSYS?
- 5. ¿Cómo puedo utilizar los resultados de la simulación de fundición en ANSYS para mejorar el proceso de fundición?
Cuáles son los materiales más adecuados para utilizar en el molde en la fundición con ANSYS
Al realizar un proceso de fundición con ANSYS, es crucial seleccionar los materiales apropiados para el molde. Estos materiales deben ser capaces de soportar altas temperaturas y resistir la presión del metal fundido. Algunas opciones comunes incluyen el acero inoxidable y las aleaciones de hierro, que son conocidas por su durabilidad y resistencia. Sin embargo, también es importante considerar la conductividad térmica de los materiales, ya que esto puede afectar la transferencia de calor durante el proceso de fundición. En general, se recomienda consultar a expertos en fundición para determinar los materiales más adecuados para cada caso específico.
Consideraciones para el diseño del molde en la fundición con ANSYS
El diseño del molde es fundamental para asegurar el éxito del proceso de fundición con ANSYS. Se deben tener en cuenta varios aspectos, como la forma y el tamaño del molde, la ubicación de los canales de llenado y el sistema de enfriamiento. El molde debe tener una geometría adecuada para permitir la correcta fluidez del metal fundido y evitar la formación de defectos, como porosidad o solidificación incompleta. Además, es importante asegurarse de que el molde sea lo suficientemente resistente para soportar las altas temperaturas y las fuerzas durante el llenado. Mediante el uso de herramientas de simulación, como ANSYS, es posible realizar análisis detallados del diseño del molde y optimizarlo para obtener los mejores resultados.
Proceso de llenado del molde en la fundición con ANSYS
El proceso de llenado del molde en la fundición con ANSYS es una etapa crítica que requiere atención minuciosa. Primero, se debe asegurar que el molde esté limpio y seco para evitar contaminaciones. Luego, se procede a calentar el metal fundido y verterlo en el canal de llenado del molde. Durante este proceso, es importante controlar la velocidad y la presión de llenado para evitar la formación de defectos, como burbujas de aire o turbulencias. ANSYS ofrece herramientas de simulación que permiten analizar y optimizar el proceso de llenado del molde, asegurando la calidad del producto final.
Qué consideraciones se deben tener en cuenta para determinar el tamaño y la forma del molde en la fundición con ANSYS
Al realizar una fundición con ANSYS, es crucial tener en cuenta varias consideraciones al determinar el tamaño y la forma del molde. Estas consideraciones pueden afectar directamente el resultado y la eficiencia del proceso de fundición.
Tamaño del molde
El tamaño del molde debe ser seleccionado cuidadosamente para garantizar que pueda contener el material fundido de manera adecuada. El tamaño debe ser lo suficientemente grande para evitar cualquier derrame o desbordamiento, pero no tan grande como para desperdiciar material y energía durante la fundición.
Forma del molde
La forma del molde también es crucial para asegurar una fundición exitosa. Debe tener la geometría adecuada para permitir un llenado uniforme y sin defectos del material fundido. La forma del molde también debe considerar las características del diseño final deseado y las limitaciones de fabricación.
Consideraciones de diseño
Además del tamaño y la forma del molde, también se deben tener en cuenta otras consideraciones de diseño. Esto incluye la ubicación y el diseño de las entradas y salidas de material, así como la inclusión de canales de enfriamiento para garantizar una solidificación adecuada y evitar defectos como la contracción.
Análisis de la fundición
Antes de decidir el tamaño y la forma del molde, es recomendable realizar un análisis de la fundición utilizando herramientas como ANSYS. Esto permite simular el proceso de fundición y evaluar el comportamiento del material fundido, identificando posibles problemas y optimizando el diseño del molde antes de su fabricación.
Iteración y mejora continua
Es importante recordar que la determinación del tamaño y la forma del molde en la fundición con ANSYS es un proceso iterativo. Es posible que se requieran varias iteraciones y ajustes para lograr un molde óptimo que garantice una fundición exitosa. La mejora continua y el análisis de los resultados obtenidos son esenciales para optimizar el proceso.
Al determinar el tamaño y la forma del molde en la fundición con ANSYS, es fundamental considerar diversos factores como el tamaño, la forma, el diseño, el análisis y la mejora continua. Estas consideraciones garantizarán una fundición exitosa y eficiente, minimizando los errores y los costos asociados.
Cuáles son las mejores prácticas para asegurar un llenado uniforme del molde en la fundición con ANSYS
El llenado del molde en la fundición es una etapa crítica del proceso, ya que afecta directamente la calidad y la integridad de la pieza fundida. En ANSYS, existen varias herramientas y técnicas que se pueden utilizar para garantizar un llenado uniforme y efectivo del molde.
1. Simulación del flujo
Una de las mejores prácticas para asegurar un llenado uniforme del molde en la fundición es realizar una simulación del flujo utilizando ANSYS. Esta simulación permite visualizar cómo el material fundido fluye dentro del molde y ayuda a identificar posibles problemas de llenado, como zonas de flujo deficiente o áreas propensas a la formación de porosidades.
2. Diseño y optimización del sistema de alimentación
Un factor clave para lograr un llenado uniforme del molde es el diseño y la optimización del sistema de alimentación. ANSYS ofrece herramientas de simulación y optimización que permiten analizar diferentes diseños de sistemas de alimentación, como canales y compuertas, para garantizar un flujo adecuado de material fundido y evitar problemas como la formación de rechupes o discontinuidades en la pieza final.
3. Control de la temperatura del molde
La temperatura del molde juega un papel importante en el llenado uniforme de la fundición. ANSYS ofrece herramientas de simulación térmica que permiten analizar y controlar la distribución de la temperatura en el molde. Esto ayuda a predecir y evitar problemas como el enfriamiento prematuro del material fundido o la formación de defectos debido a gradientes de temperatura excesivos.
4. Optimización de la velocidad de llenado
La velocidad de llenado del molde también influye en la uniformidad del llenado. ANSYS ofrece herramientas de simulación que permiten analizar y optimizar la velocidad de llenado para evitar problemas como la formación de remolinos o la falta de material en ciertas áreas del molde. Una velocidad de llenado adecuada garantiza una distribución uniforme del material fundido y reduce la probabilidad de defectos en la pieza final.
5. Análisis de la solidificación y contracción
La solidificación y contracción del material fundido son aspectos críticos a tener en cuenta para asegurar un llenado uniforme del molde en la fundición. ANSYS ofrece herramientas de simulación que permiten analizar el proceso de solidificación y contracción y predecir posibles problemas, como la formación de porosidades debido a una contracción excesiva. Esto ayuda a optimizar los parámetros del proceso de fundición y garantizar un llenado uniforme del molde.
Para asegurar un llenado uniforme del molde en la fundición con ANSYS, es importante realizar una simulación del flujo, diseñar y optimizar el sistema de alimentación, controlar la temperatura del molde, optimizar la velocidad de llenado y analizar la solidificación y contracción del material fundido. Estas prácticas garantizan un resultado de alta calidad y reducen la probabilidad de defectos en la pieza final.
Existen técnicas especiales para evitar defectos de llenado en el molde en la fundición con ANSYS
La fundición con ANSYS es un proceso complejo que requiere técnicas especiales para evitar defectos de llenado en el molde. Estos defectos pueden afectar la calidad y la integridad de la pieza fundida, lo que a su vez puede comprometer su desempeño y durabilidad.
Uno de los pasos efectivos para llenar el molde en la fundición con ANSYS es la optimización del diseño del sistema de llenado. Esto implica analizar y mejorar la geometría del sistema de alimentación y los canales de flujo para asegurar un llenado uniforme y sin obstrucciones.
Otro paso clave es la simulación del llenado utilizando el software ANSYS. Esta herramienta permite visualizar el proceso de llenado en tiempo real, identificar posibles puntos problemáticos y realizar ajustes en el diseño antes de producir la pieza. La simulación también ayuda a predecir y evitar defectos como la formación de porosidades, cavidades o inclusiones en la pieza final.
Además, es importante tener en cuenta las propiedades del material y su comportamiento durante el proceso de fundición. ANSYS permite simular y analizar estas propiedades, lo que ayuda a optimizar los parámetros de fundición, como la temperatura, la velocidad de llenado y la presión, para evitar defectos de llenado.
Finalmente, es fundamental realizar pruebas y ajustes en el proceso de fundición con ANSYS para validar las simulaciones y garantizar la calidad de la pieza final. Esto puede incluir la realización de pruebas de llenado en moldes de prueba y la comparación de los resultados con las simulaciones realizadas previamente.
Seguir estos pasos efectivos para llenar el molde en la fundición con ANSYS puede ayudar a evitar defectos de llenado y garantizar la calidad de las piezas fundidas. La combinación de la optimización del diseño, la simulación del llenado, el análisis de las propiedades del material y las pruebas de validación es clave para lograr resultados exitosos en la fundición con ANSYS.
Cómo se puede optimizar el tiempo de llenado del molde en la fundición con ANSYS
La fundición es un proceso esencial en la fabricación de piezas metálicas, pero el tiempo de llenado del molde puede ser un factor crucial en la eficiencia de producción. ANSYS es un software de simulación ampliamente utilizado en la industria para predecir y optimizar el proceso de fundición.
Para optimizar el tiempo de llenado del molde en la fundición con ANSYS, es importante seguir algunos pasos efectivos. En primer lugar, es necesario realizar un análisis detallado de la geometría del molde y sus canales de llenado. Esto permitirá identificar posibles áreas de estrangulamiento o flujo no uniforme.
Análisis de flujo
Utilizando las capacidades de simulación de ANSYS, se puede realizar un análisis de flujo para predecir cómo se distribuirá el metal fundido dentro del molde. Esto proporcionará información valiosa sobre los puntos críticos de flujo y ayudará a optimizar el diseño del sistema de llenado.
Es importante considerar la velocidad de llenado del molde. Una velocidad demasiado alta puede generar turbulencias y defectos en la pieza final, mientras que una velocidad baja puede prolongar innecesariamente el tiempo de llenado. ANSYS permite simular diferentes velocidades de llenado y evaluar su impacto en la calidad de la pieza.
Diseño de los canales de llenado
El diseño de los canales de llenado es fundamental para garantizar un flujo uniforme de metal fundido en el molde. ANSYS ofrece herramientas de diseño que permiten optimizar la forma y dimensiones de los canales, minimizando la resistencia al flujo y maximizando la eficiencia del llenado.
Es recomendable utilizar geometrías suaves y transiciones gradual en los canales de llenado para evitar puntos de estrangulamiento o turbulencias. ANSYS permite evaluar diferentes diseños y encontrar la configuración óptima que garantice un llenado uniforme y rápido del molde.
Validación mediante simulaciones
Una vez que se ha realizado el diseño y optimización del sistema de llenado del molde en ANSYS, es crucial validar su rendimiento mediante simulaciones detalladas. Estas simulaciones permiten evaluar el flujo de metal fundido en condiciones reales y predecir posibles defectos o áreas problemáticas.
La validación de las simulaciones se realiza comparando los resultados con datos experimentales o con piezas ya fabricadas. Esto permitirá ajustar y mejorar el diseño antes de la producción en serie, asegurando un llenado efectivo y eficiente del molde.
Para optimizar el tiempo de llenado del molde en la fundición con ANSYS es necesario realizar un análisis detallado de la geometría del molde, simular el flujo de metal fundido, diseñar de forma adecuada los canales de llenado y validar los resultados mediante simulaciones detalladas.
El uso de ANSYS como herramienta de simulación permite optimizar el proceso de fundición, reducir los tiempos de llenado y mejorar la calidad de las piezas fabricadas. Siguiendo estos pasos efectivos, los fabricantes pueden aumentar la eficiencia de producción y minimizar los costos asociados.
Qué estrategias se pueden implementar para reducir los costos de fabricación en la fundición con ANSYS
La fundición es un proceso clave en la fabricación de piezas metálicas, y maximizar la eficiencia y minimizar los costos son aspectos fundamentales. En este sentido, ANSYS es una herramienta poderosa que puede ayudar a optimizar el llenado del molde durante el proceso de fundición.
Para reducir los costos de fabricación en la fundición con ANSYS, se pueden implementar diversas estrategias. En primer lugar, es crucial utilizar un diseño de molde adecuado. Esto implica tener en cuenta la geometría de la pieza a fundir, así como los canales de llenado y enfriamiento. ANSYS permite simular diferentes diseños y analizar su eficiencia, lo que puede ayudar a seleccionar la mejor opción.
Otra estrategia efectiva es optimizar los parámetros de llenado. ANSYS permite modelar el flujo del metal líquido en el molde y analizar variables como la velocidad de llenado, la temperatura y la presión. A través de la simulación, es posible identificar los puntos críticos donde puede haber defectos, como poros o inclusiones, y ajustar los parámetros para minimizar su aparición.
Código de ejemplo:
// Definición de variables
int temperatura = 1500;
double presion = 200;
double velocidad = 0.5;
// Simulación de llenado del molde
ANSYS.simularLlenado(temperatura, presion, velocidad);
// Análisis de resultados
ANSYS.analizarDefectos();
Además, es importante considerar la elección de los materiales. ANSYS permite analizar el comportamiento de diferentes aleaciones metálicas durante el proceso de fundición, lo que puede ayudar a seleccionar el material óptimo en términos de costo y calidad. Asimismo, ANSYS permite evaluar la influencia de variables como la temperatura y la velocidad de enfriamiento en las propiedades del material final.
Por último, es fundamental tener en cuenta la optimización del tiempo de fundición. ANSYS permite simular diferentes escenarios y analizar el tiempo requerido para llenar el molde de manera eficiente. De esta forma, es posible identificar cuellos de botella y realizar ajustes en el proceso para reducir los tiempos de producción y, por ende, los costos asociados.
La implementación de estrategias efectivas para reducir los costos de fabricación en la fundición con ANSYS puede ser de gran beneficio para las empresas. La simulación y análisis de diferentes variables, como el diseño del molde, los parámetros de llenado, la elección de materiales y el tiempo de fundición, son aspectos clave que pueden ayudar a optimizar el proceso y obtener piezas de alta calidad a un menor costo.
Cuáles son las principales dificultades o desafíos que pueden surgir al llenar el molde en la fundición con ANSYS
Al utilizar el software ANSYS para llenar el molde en el proceso de fundición, pueden surgir diversos desafíos y dificultades. Uno de los problemas comunes es la formación de porosidad en la pieza fundida. Esto puede ocurrir debido a un llenado inadecuado del molde, lo que resulta en áreas con aire atrapado. Para evitar este problema, es importante garantizar un flujo de metal uniforme y adecuado en todas las áreas del molde.
Otro desafío que puede surgir es la formación de contracción en la pieza fundida. La contracción es una reducción en el volumen del metal fundido a medida que se enfría y solidifica. Para evitar este problema, se deben tener en cuenta diversos factores, como la temperatura del metal fundido, la ubicación de las entradas de llenado y la geometría del molde.
Importancia de realizar un análisis de flujo en la fundición con ANSYS
Realizar un análisis de flujo en la fundición con ANSYS es de vital importancia para garantizar la calidad y la integridad de la pieza fundida. Este tipo de análisis permite simular y predecir el comportamiento del metal fundido durante el llenado del molde, lo que ayuda a identificar posibles problemas y tomar las medidas necesarias para evitarlos.
El análisis de flujo en la fundición con ANSYS proporciona información sobre la velocidad de llenado del molde, la ubicación de los puntos calientes, la formación de porosidad y contracción, entre otros aspectos críticos. Esto permite realizar ajustes en el diseño del molde y en los parámetros de colada para optimizar el proceso de fundición y obtener piezas de alta calidad.
Principales pasos para llenar el molde en la fundición con ANSYS
- Preparar el modelo de fundición: esto implica la creación del modelo 3D del molde y la pieza a fundir. Se deben definir los materiales, las condiciones de enfriamiento y los puntos de llenado.
- Definir las entradas de llenado: se deben identificar las ubicaciones estratégicas para las entradas de metal fundido en el molde. Esto puede incluir la creación de canales de alimentación y la determinación de la posición de las compuertas de llenado.
- Establecer las condiciones de llenado: se deben definir las propiedades del metal fundido, como la viscosidad y la temperatura, así como las condiciones de enfriamiento durante el proceso de llenado.
- Ejecutar la simulación: una vez que se han definido todos los parámetros, se debe ejecutar la simulación en ANSYS. Esto permitirá visualizar el llenado del molde y obtener información sobre la distribución del metal fundido.
- Analizar los resultados: una vez completada la simulación, se deben analizar los resultados obtenidos para identificar posibles problemas, como la formación de porosidad o contracción. En base a estos resultados, se pueden realizar ajustes en el diseño del molde o en los parámetros de colada.
- Optimizar el proceso: con la información obtenida de la simulación, se pueden realizar mejoras en el diseño del molde y en el proceso de colada para optimizar la calidad de la pieza fundida. Esto puede incluir cambios en la ubicación de las entradas de llenado, en la geometría del molde o en las condiciones de enfriamiento.
Llenar el molde en la fundición con ANSYS requiere de un análisis de flujo meticuloso y la realización de diversos pasos clave. Al seguir estos pasos y hacer uso de las capacidades de simulación de ANSYS, se pueden evitar problemas como la porosidad y la contracción, y obtener piezas de alta calidad en el proceso de fundición.
Qué métodos de análisis y simulación se pueden utilizar para evaluar la calidad del llenado del molde en la fundición con ANSYS
El llenado del molde en el proceso de fundición puede tener un impacto significativo en la calidad final de la pieza fundida. Por lo tanto, es crucial utilizar métodos de análisis y simulación precisos para evaluar la eficacia del llenado del molde en la fundición con ANSYS.
Un método comúnmente utilizado es la simulación numérica del flujo de llenado del molde. Esto implica modelar el molde y el flujo de metal fundido utilizando software de simulación como ANSYS. Mediante el uso de ecuaciones matemáticas y técnicas de simulación avanzadas, es posible predecir cómo se llenará el molde y evaluar la calidad del llenado.
La simulación del flujo de llenado del molde con ANSYS permite identificar posibles problemas como la formación de porosidades, la falta de llenado en ciertas áreas o la formación de rechupes. Estos problemas pueden afectar la integridad estructural y la funcionalidad de la pieza fundida, por lo que es crucial detectarlos y corregirlos antes de la producción en masa.
Además de la simulación numérica, ANSYS también ofrece herramientas de análisis térmico y de solidificación. Estas permiten evaluar aspectos como la distribución de temperaturas en el molde durante el llenado, la velocidad de solidificación y la formación de estructuras de solidificación no deseables como las dendritas. Esta información es clave para optimizar los parámetros de fundición y mejorar la calidad de las piezas fundidas.
Los métodos de análisis y simulación que se pueden utilizar para evaluar la calidad del llenado del molde en la fundición con ANSYS son la simulación numérica del flujo de llenado, el análisis térmico y el análisis de solidificación. Estas herramientas permiten detectar posibles problemas de llenado, evaluar la distribución de temperaturas y optimizar los parámetros de fundición para mejorar la calidad de las piezas fundidas.
Es posible realizar modificaciones en el diseño del molde durante el proceso de llenado en la fundición con ANSYS
La fundición con ANSYS ofrece una gran flexibilidad al permitir realizar modificaciones en el diseño del molde durante el proceso de llenado. Esto es especialmente útil cuando se requiere realizar ajustes en tiempo real para mejorar la calidad del producto final.
Para realizar modificaciones en el diseño del molde durante el proceso de llenado en la fundición con ANSYS, es necesario seguir algunos pasos efectivos. En primer lugar, es importante tener claridad sobre los cambios que se desean realizar y cómo se espera que estos afecten el proceso.
Análisis de la simulación previa
Antes de realizar cualquier modificación en el diseño del molde, es fundamental analizar detalladamente los resultados de la simulación previa. Esto permitirá identificar los puntos clave que necesitan ser mejorados y determinar cómo los cambios en el diseño del molde pueden contribuir a una fundición más efectiva.
La simulación previa proporciona información valiosa sobre el comportamiento del material durante el llenado del molde. Esto incluye la distribución de temperatura, la presión y la velocidad de flujo. Al analizar estos resultados, es posible identificar zonas donde se podrían presentar defectos en la pieza fundida y así determinar los cambios necesarios en el diseño del molde.
Optimización del diseño
Una vez que se ha realizado el análisis de la simulación previa, es hora de optimizar el diseño del molde. Esto implica hacer ajustes en la geometría del molde para mejorar la distribución de temperatura, reducir la presión o ajustar la velocidad de flujo del material fundido.
Es importante tener en cuenta que realizar cambios en el diseño del molde durante el proceso de llenado puede tener un impacto significativo en la calidad del producto final. Por lo tanto, es necesario realizar pruebas adicionales para asegurarse de que los cambios propuestos sean efectivos y no introduzcan nuevos problemas.
Implementación de las modificaciones
Una vez que se ha optimizado el diseño del molde, es hora de implementar las modificaciones en el proceso de llenado. Esto implica realizar los cambios necesarios en el diseño del molde y volver a ejecutar la simulación para evaluar los resultados.
Es importante tener en cuenta que la implementación de modificaciones en el diseño del molde puede requerir tiempo adicional y recursos. Sin embargo, los beneficios de realizar ajustes en tiempo real durante el proceso de llenado pueden ser significativos, ya que permiten mejorar la calidad del producto final y optimizar el rendimiento del proceso de fundición.
La fundición con ANSYS ofrece la posibilidad de realizar modificaciones en el diseño del molde durante el proceso de llenado. Para ello, es necesario realizar un análisis detallado de la simulación previa, optimizar el diseño del molde y finalmente implementar las modificaciones en el proceso de llenado. Estos pasos efectivos permiten mejorar la calidad del producto final y optimizar el rendimiento del proceso de fundición.
Cuáles son los beneficios de utilizar la simulación en la fundición con ANSYS en comparación con los métodos convencionales
La simulación en la fundición con ANSYS ofrece una serie de beneficios significativos en comparación con los métodos convencionales utilizados anteriormente. En primer lugar, permite a los ingenieros predecir y evaluar con precisión el comportamiento de los moldes durante el proceso de llenado, lo que les permite realizar ajustes necesarios para optimizar la calidad del producto final.
Además, ANSYS proporciona una representación visual detallada de la distribución de temperatura y flujo de metal líquido en el molde, lo que ayuda a identificar posibles problemas como inclusiones, porosidad o defectos de llenado. Esto permite a los ingenieros tomar decisiones informadas sobre la geometría del molde y los parámetros de fundición antes de iniciar el proceso físico.
Otro beneficio clave es la reducción de costos y tiempos de producción. Al simular el llenado del molde con ANSYS, los ingenieros pueden optimizar la ubicación y diseño de los sistemas de alimentación, minimizando las pérdidas de metal y reduciendo el período de prueba-error. Además, se pueden realizar análisis de solidificación y enfriamiento, lo que ayuda a predecir y prevenir defectos relacionados con el proceso de enfriamiento.
La utilización de la simulación en la fundición con ANSYS brinda a los ingenieros una valiosa herramienta para mejorar la calidad del producto, reducir costos y tiempos de producción, y tomar decisiones informadas basadas en datos precisos y confiables. Con su capacidad para predecir el comportamiento del molde y el flujo de metal líquido, ANSYS se ha convertido en una solución efectiva y confiable en el campo de la fundición.
Preguntas frecuentes (FAQ)
1. ¿Cuál es el proceso para llenar el molde en la fundición con ANSYS?
El proceso para llenar el molde en la fundición con ANSYS implica activar la opción de simulación de fundición, definir las propiedades del material y la geometría del molde, establecer las condiciones iniciales y de contorno, y ejecutar la simulación.
2. ¿Qué parámetros debo considerar al realizar la simulación de fundición con ANSYS?
Al realizar la simulación de fundición con ANSYS, debes considerar la temperatura del material fundido, la velocidad y dirección de llenado, la conductividad térmica del molde, y las condiciones de enfriamiento.
3. ¿Cómo puedo verificar si el llenado del molde en la simulación de fundición es correcto?
Puedes verificar si el llenado del molde en la simulación de fundición es correcto observando el patrón de llenado en la interfaz gráfica, y analizando la distribución de temperatura y presión en el sistema. Además, puedes realizar pruebas de solidificación para evaluar la formación de defectos.
4. ¿Qué tipos de defectos de fundición puedo prevenir con la simulación de fundición en ANSYS?
La simulación de fundición en ANSYS te permite prevenir defectos como porosidad, segregación, contracción y agrietamiento, al simular y optimizar el proceso de llenado del molde, y controlar las condiciones de solidificación y enfriamiento.
5. ¿Cómo puedo utilizar los resultados de la simulación de fundición en ANSYS para mejorar el proceso de fundición?
Los resultados de la simulación de fundición en ANSYS te permiten identificar áreas problemáticas en el proceso de fundición, optimizar el diseño del molde y las condiciones de llenado, y ajustar los parámetros de fundición para mejorar la calidad y eficiencia del proceso.
Deja una respuesta
Entradas relacionadas