Realiza un análisis de recipientes a presión con ANSYS: guía completa
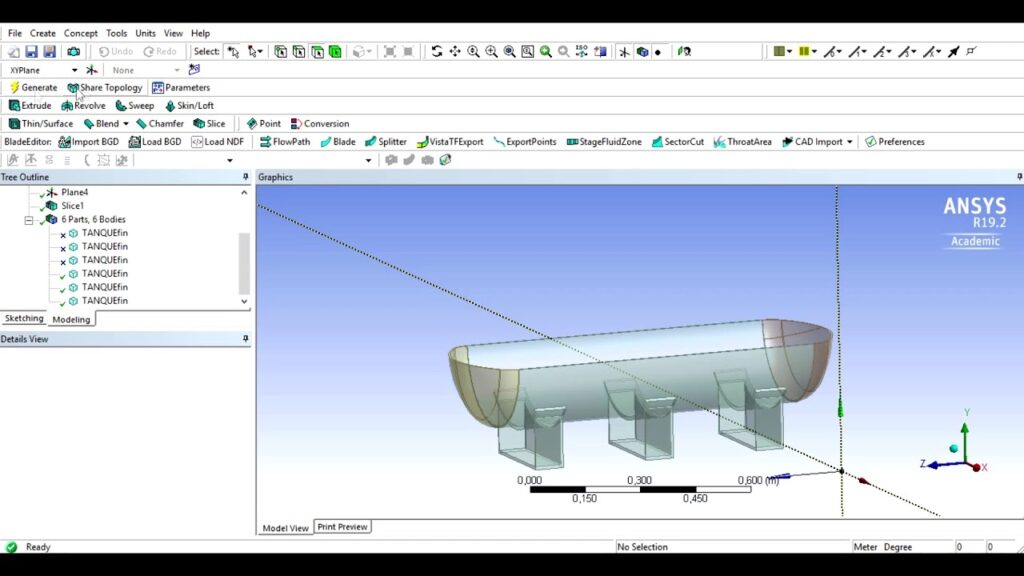
En el ámbito de la ingeniería, los recipientes a presión son elementos fundamentales para el almacenamiento y transporte de sustancias a presiones elevadas. Estos recipientes están sometidos a fuerzas internas y externas que pueden generar tensiones y deformaciones, por lo que es crucial realizar un análisis riguroso para garantizar su seguridad y eficiencia.
Te presentaremos una guía completa sobre cómo realizar un análisis de recipientes a presión utilizando el software ANSYS. Exploraremos los conceptos clave del análisis de recipientes a presión, los pasos necesarios para llevar a cabo la simulación y los resultados que se pueden obtener. Además, discutiremos las ventajas de utilizar ANSYS en este tipo de análisis y cómo se pueden utilizar los resultados para optimizar el diseño y mejorar la calidad de los recipientes a presión. Si eres ingeniero o estudiante de ingeniería interesado en el análisis de recipientes a presión, ¡sigue leyendo!
- Cuáles son las ventajas de utilizar ANSYS para el análisis de recipientes a presión
- Qué es un recipiente a presión y por qué es importante realizar su análisis
- Cuáles son los principales desafíos en el análisis de recipientes a presión
- Cuál es el proceso paso a paso para realizar un análisis de recipientes a presión con ANSYS
- Paso 1: Preparación de la geometría del recipiente a presión
- Paso 2: Importar la geometría a ANSYS
- Paso 3: Aplicar condiciones de contorno y materiales
- Paso 4: Generar la malla de elementos finitos
- Paso 5: Definir y ejecutar el análisis
- Paso 6: Interpretar y analizar los resultados
- Paso 7: Optimizar el diseño del recipiente a presión
- Paso 8: Verificar y validar los resultados
- Paso 9: Documentar y comunicar los resultados
- Cuáles son las herramientas y funcionalidades clave de ANSYS para el análisis de recipientes a presión
- Existen alternativas a ANSYS para el análisis de recipientes a presión? ¿Cuáles son y cómo se comparan con ANSYS
- Cuáles son los errores comunes a evitar al realizar un análisis de recipientes a presión con ANSYS
- Cuál es la importancia de la validación y verificación de los resultados en el análisis de recipientes a presión
- Cuáles son los beneficios y aplicaciones del análisis de recipientes a presión con ANSYS en diferentes industrias
- Existen estudios de caso o ejemplos reales de análisis de recipientes a presión con ANSYS que demuestren su eficacia y precisión
- Preguntas frecuentes (FAQ)
- 1. ¿Qué es un recipiente a presión?
- 2. ¿Por qué es importante realizar un análisis de recipientes a presión?
- 3. ¿Cómo se realiza un análisis de recipientes a presión con ANSYS?
- 4. ¿Cuáles son los tipos de análisis que se pueden realizar con ANSYS?
- 5. ¿Cuáles son los beneficios de utilizar ANSYS para el análisis de recipientes a presión?
Cuáles son las ventajas de utilizar ANSYS para el análisis de recipientes a presión
ANSYS es una herramienta de simulación ampliamente utilizada en la ingeniería para realizar análisis de recipientes a presión. Esta plataforma ofrece una serie de ventajas que la hacen una opción popular entre los profesionales de la industria.
En primer lugar, ANSYS brinda una amplia gama de capacidades para simular el comportamiento de recipientes a presión en diferentes condiciones y escenarios. Esto permite a los ingenieros evaluar y predecir de manera precisa cómo estos recipientes responderán frente a diferentes cargas y presiones.
Otra ventaja importante de utilizar ANSYS es su capacidad para modelar y analizar la transferencia de calor en los recipientes a presión. Esto es crucial para determinar cómo se distribuye el calor en el interior del recipiente y cómo afecta su integridad estructural.
Además, ANSYS ofrece la posibilidad de simular el flujo de fluidos y gases dentro de los recipientes a presión. Esta capacidad es esencial para evaluar cómo se comportará el fluido en condiciones reales y cómo esto puede afectar el rendimiento y la vida útil del recipiente.
ANSYS también permite realizar análisis de fatiga y evaluaciones de vida útil en los recipientes a presión. Estas herramientas ayudan a los ingenieros a identificar áreas críticas de alta tensión y predecir la vida útil de los recipientes en condiciones de carga repetitiva.
Finalmente, ANSYS ofrece una interfaz amigable y fácil de usar que permite a los ingenieros realizar análisis de recipientes a presión de manera eficiente y precisa. Esto hace que la herramienta sea accesible para usuarios de diferentes niveles de experiencia en el campo de la ingeniería.
Utilizar ANSYS para el análisis de recipientes a presión ofrece una serie de ventajas, como la capacidad de simular diferentes condiciones y escenarios, modelar la transferencia de calor, analizar el flujo de fluidos y gases, realizar análisis de fatiga y evaluar la vida útil de los recipientes. Además, la interfaz amigable de ANSYS hace que sea una opción accesible y eficiente para los ingenieros.
Qué es un recipiente a presión y por qué es importante realizar su análisis
Un recipiente a presión es un contenedor diseñado para contener gases o líquidos a una presión interna mayor que la presión atmosférica. Estos recipientes se utilizan en una amplia variedad de industrias, como la petroquímica, la alimentaria y la farmacéutica, entre otras. Es importante realizar un análisis exhaustivo de estos recipientes para garantizar su seguridad y eficiencia.
El análisis de recipientes a presión implica evaluar su resistencia estructural, su capacidad para soportar la presión interna y externa, así como su capacidad para resistir las fuerzas externas, como el viento o los terremotos. Además, también es necesario evaluar la estabilidad del recipiente y su capacidad para evitar fugas o fallas catastróficas.
Realizar un análisis de recipientes a presión con ANSYS es una opción altamente recomendada. ANSYS es un software de simulación por elementos finitos ampliamente utilizado en ingeniería. Permite simular y analizar de manera precisa y detallada el comportamiento de los recipientes a presión, teniendo en cuenta factores como materiales, dimensiones, condiciones de carga y restricciones.
Al realizar un análisis de recipientes a presión con ANSYS, se puede obtener información valiosa sobre la resistencia del recipiente, identificar áreas de alta tensión y predecir posibles puntos de falla. Esto permite realizar mejoras en el diseño y tomar decisiones informadas para garantizar la seguridad y eficiencia del recipiente.
Pasos para realizar un análisis de recipientes a presión con ANSYS
- Definir las propiedades y dimensiones del recipiente a presión. Esto incluye especificar el tipo de material, el espesor de las paredes, las dimensiones del recipiente, entre otros.
- Establecer las condiciones de carga. Esto implica definir la presión interna y externa a las que estará sometido el recipiente, así como las fuerzas externas que actuarán sobre él.
- Crear el modelo de elementos finitos en ANSYS. Esto implica dividir el recipiente en elementos más pequeños para poder analizar su comportamiento de manera más detallada. Se deben asignar propiedades y restricciones a cada elemento.
- Aplicar las condiciones de carga al modelo. Esto implica aplicar la presión interna y externa, así como las fuerzas externas, al modelo de elementos finitos.
- Ejecutar el análisis en ANSYS. Esto implica resolver las ecuaciones matemáticas que describen el comportamiento del recipiente bajo las condiciones de carga establecidas.
- Analizar los resultados del análisis. Esto implica revisar los resultados obtenidos en ANSYS, como las tensiones, deformaciones y desplazamientos del recipiente.
- Realizar mejoras en el diseño si es necesario. Si se identifican áreas de alta tensión o posibles puntos de falla, se deben realizar modificaciones en el diseño del recipiente para garantizar su seguridad.
Realizar un análisis de recipientes a presión con ANSYS es fundamental para garantizar la seguridad y eficiencia de estos contenedores. A través de pasos como la definición de propiedades, la aplicación de condiciones de carga y la ejecución del análisis en ANSYS, se pueden obtener resultados precisos y detallados sobre el comportamiento de los recipientes. Esto permite tomar decisiones informadas y realizar mejoras en el diseño para garantizar su correcto funcionamiento.
Cuáles son los principales desafíos en el análisis de recipientes a presión
El análisis de recipientes a presión es una parte crucial en el diseño y fabricación de equipos industriales. Estos recipientes están diseñados para contener sustancias a presiones extremas, por lo que es fundamental garantizar su integridad y seguridad. Sin embargo, el análisis de recipientes a presión presenta varios desafíos que deben abordarse adecuadamente.
Uno de los principales desafíos en el análisis de recipientes a presión es la determinación de las cargas internas y externas que actúan sobre el recipiente. Estas cargas incluyen la presión interna, la tensión térmica, las cargas estáticas y las cargas dinámicas. Además, también se deben considerar factores como la corrosión, la fatiga y la fragilidad en el análisis.
Otro desafío importante es la modelización del recipiente y sus componentes. Es necesario crear un modelo preciso y detallado que represente de manera adecuada la geometría y las características del recipiente. Esto implica considerar los materiales utilizados, las soldaduras, los refuerzos y las conexiones, entre otros aspectos.
Además, el análisis de recipientes a presión requiere de una buena comprensión de las leyes de la física y de las teorías de resistencia de materiales. Es fundamental aplicar estos conocimientos de manera adecuada para interpretar los resultados del análisis y tomar decisiones informadas sobre el diseño y las modificaciones necesarias.
La interpretación de los resultados y la toma de decisiones también puede ser un desafío en el análisis de recipientes a presión. Los resultados obtenidos a partir del análisis pueden ser complejos y requerir una cuidadosa consideración. Es necesario evaluar si el recipiente es capaz de soportar las cargas a las que estará expuesto durante su vida útil y si se requieren modificaciones en el diseño para garantizar su seguridad.
El análisis de recipientes a presión presenta varios desafíos que deben ser abordados de manera adecuada. Es fundamental comprender y considerar las cargas internas y externas, modelar de manera precisa el recipiente, aplicar los conocimientos de resistencia de materiales y tomar decisiones informadas a partir de los resultados obtenidos. Solo así se puede garantizar la integridad y seguridad de estos importantes equipos industriales.
Cuál es el proceso paso a paso para realizar un análisis de recipientes a presión con ANSYS
Realizar un análisis de recipientes a presión con ANSYS puede ser una tarea compleja, pero siguiendo un proceso paso a paso, puedes obtener resultados precisos y confiables. A continuación, te presentamos la guía completa para llevar a cabo este proceso:
Paso 1: Preparación de la geometría del recipiente a presión
En primer lugar, debes obtener la geometría del recipiente a presión que deseas analizar. Esto se puede hacer mediante el modelado 3D en software de diseño asistido por computadora como SolidWorks. Es importante asegurarse de que la geometría esté completa y sin errores.
Paso 2: Importar la geometría a ANSYS
Una vez que tienes la geometría del recipiente a presión, debes importarla a ANSYS. Esto se puede hacer utilizando el módulo de geometría de ANSYS, donde puedes importar archivos en diferentes formatos, como STEP o IGES. Asegúrate de que la geometría se importe correctamente y de que esté en la escala adecuada.
Paso 3: Aplicar condiciones de contorno y materiales
Una vez que la geometría está importada en ANSYS, debes aplicar las condiciones de contorno y los materiales necesarios para el análisis. Esto implica definir las restricciones, como apoyos y cargas, así como la asignación de propiedades de los materiales, como el módulo de elasticidad y la densidad. Esto se puede hacer utilizando las herramientas de simulación de ANSYS.
Paso 4: Generar la malla de elementos finitos
Una vez que se han aplicado las condiciones de contorno y los materiales, debes generar la malla de elementos finitos. La malla es una discretización de la geometría en pequeños elementos, donde se realizarán los cálculos. ANSYS ofrece diferentes tipos de elementos finitos, como elementos tetraédricos o hexaédricos, que se pueden utilizar según la geometría del recipiente a presión.
Paso 5: Definir y ejecutar el análisis
Con la malla de elementos finitos generada, debes definir y ejecutar el análisis en ANSYS. Esto implica seleccionar el tipo de análisis que deseas realizar, como un análisis estático o un análisis de fatiga, y configurar las opciones correspondientes, como el número de iteraciones y la precisión deseada. Una vez que todo esté configurado, puedes ejecutar el análisis y obtener los resultados.
Paso 6: Interpretar y analizar los resultados
Una vez que el análisis haya finalizado, debes interpretar y analizar los resultados obtenidos. Esto implica revisar las deformaciones, las tensiones y otras variables relevantes para evaluar el comportamiento del recipiente a presión. ANSYS ofrece herramientas de postprocesamiento que te permiten visualizar y analizar los resultados de manera eficiente.
Paso 7: Optimizar el diseño del recipiente a presión
Si los resultados del análisis indican que el recipiente a presión no cumple con los requisitos de diseño, puedes utilizar los resultados y las herramientas de optimización de ANSYS para mejorar la geometría y el rendimiento del recipiente. Esto puede implicar modificar la geometría, cambiar los materiales o ajustar las condiciones de contorno.
Paso 8: Verificar y validar los resultados
Una vez que hayas optimizado el diseño del recipiente a presión, debes verificar y validar los resultados obtenidos. Esto implica realizar pruebas físicas, como pruebas de carga, para comparar los resultados obtenidos en ANSYS con los resultados experimentales. Esto te ayudará a verificar la confiabilidad y precisión de tu análisis en ANSYS.
Paso 9: Documentar y comunicar los resultados
Finalmente, debes documentar y comunicar los resultados obtenidos en el análisis de recipientes a presión con ANSYS. Esto implica elaborar informes técnicos detallados que incluyan los pasos seguidos, los resultados obtenidos y las conclusiones alcanzadas. También es importante comunicar los resultados de manera efectiva a los stakeholders relevantes, como ingenieros de diseño y gerentes de proyectos.
Realizar un análisis de recipientes a presión con ANSYS requiere seguir un proceso paso a paso que involucra la preparación de la geometría, la importación de la geometría a ANSYS, la aplicación de condiciones de contorno y materiales, la generación de la malla de elementos finitos, la definición y ejecución del análisis, la interpretación y análisis de los resultados, la optimización del diseño, la verificación y validación de los resultados, y la documentación y comunicación de los resultados. Siguiendo esta guía completa, podrás llevar a cabo análisis de recipientes a presión de manera eficiente y confiable con ANSYS.
Cuáles son las herramientas y funcionalidades clave de ANSYS para el análisis de recipientes a presión
ANSYS es un software de simulación líder en la industria que ofrece una amplia gama de herramientas y funcionalidades para el análisis de recipientes a presión. Estas herramientas permiten a los ingenieros evaluar y optimizar el rendimiento de los recipientes a presión, garantizando su seguridad y cumplimiento de los estándares internacionales.
Una de las herramientas clave de ANSYS para el análisis de recipientes a presión es la capacidad de modelar y simular las condiciones de carga y presión a las que se someterá el recipiente. Esto incluye la capacidad de definir la geometría del recipiente, las condiciones de contorno y las cargas aplicadas.
Además, ANSYS ofrece capacidades avanzadas de análisis estructural y térmico para evaluar el comportamiento del recipiente bajo diferentes escenarios de carga y temperatura. Esto incluye la capacidad de realizar análisis estáticos y dinámicos, así como análisis de fatiga y deformación.
Otra funcionalidad importante de ANSYS es la capacidad de realizar análisis de flujo de fluidos dentro del recipiente a presión. Esto permite evaluar el comportamiento del flujo, la distribución de la presión y la acumulación de calor en el recipiente.
Además de las herramientas de análisis, ANSYS también ofrece capacidades de postprocesamiento que permiten visualizar y analizar los resultados de las simulaciones. Esto incluye la capacidad de generar gráficos, tablas y animaciones para facilitar la interpretación de los resultados.
ANSYS proporciona a los ingenieros las herramientas y funcionalidades necesarias para realizar un análisis completo y detallado de recipientes a presión. Desde la modelización y simulación de las condiciones de carga y presión hasta el análisis estructural, térmico y de flujo, ANSYS ofrece una solución integral para garantizar la seguridad y el rendimiento óptimo de los recipientes a presión.
Existen alternativas a ANSYS para el análisis de recipientes a presión? ¿Cuáles son y cómo se comparan con ANSYS
Sin duda, ANSYS es una herramienta líder en el análisis de recipientes a presión, pero existen alternativas viables que pueden resultar igualmente eficientes para ciertas aplicaciones. Entre estas alternativas se encuentran software como COMSOL Multiphysics, Abaqus y Siemens NX, por mencionar solo algunos.
COMSOL Multiphysics es conocido por su enfoque en la simulación multiphysics, lo que lo convierte en una excelente opción para aquellos que buscan un análisis detallado de los efectos acoplados de diferentes fenómenos físicos en los recipientes a presión. Por otro lado, Abaqus es una herramienta ampliamente utilizada en la industria y cuenta con una amplia gama de capacidades de modelado y análisis estructural.
Siemens NX también merece ser mencionado, ya que ofrece una solución completa para el diseño y análisis de recipientes a presión. Además, su capacidad para la integración con otras etapas de diseño y fabricación hace que sea una opción atractiva para aquellos que buscan un flujo de trabajo más integrado.
Comparación con ANSYS
Si bien estas alternativas ofrecen capacidades similares al análisis de recipientes a presión, es importante considerar las diferencias en términos de funcionalidad, complejidad y costos entre ellas y ANSYS.
ANSYS es conocido por su amplia gama de funcionalidades y capacidades avanzadas, lo que lo convierte en una opción preferida para aplicaciones complejas y análisis detallados. Además, su larga trayectoria en la industria le ha dado una sólida reputación y una amplia base de usuarios que pueden brindar soporte y experiencia.
En términos de complejidad, ANSYS puede requerir un tiempo de aprendizaje más largo debido a su amplio espectro de capacidades. Sin embargo, su interfaz intuitiva y fácil de usar ayuda a reducir la curva de aprendizaje.
En cuanto a los costos, ANSYS puede ser más costoso en comparación con algunas de las alternativas mencionadas. Sin embargo, es importante tener en cuenta que los costos pueden variar según las necesidades específicas de cada usuario y las licencias disponibles.
Si estás buscando alternativas a ANSYS para el análisis de recipientes a presión, opciones como COMSOL Multiphysics, Abaqus y Siemens NX pueden ser consideradas. Cada una tiene sus propias fortalezas y debilidades, y es importante evaluar tus necesidades específicas antes de tomar una decisión. Ten en cuenta la funcionalidad, complejidad y costos para determinar cuál de estas opciones se adapta mejor a tus requerimientos.
Cuáles son los errores comunes a evitar al realizar un análisis de recipientes a presión con ANSYS
Al realizar un análisis de recipientes a presión con ANSYS, es importante tener en cuenta algunos errores comunes que pueden surgir durante el proceso. Estos errores pueden afectar la precisión y confiabilidad de los resultados obtenidos, por lo que es fundamental evitarlos. A continuación, se presentan algunos de los errores más comunes y cómo evitarlos:
No considerar la geometría real del recipiente:
Uno de los errores más comunes es no tener en cuenta la geometría real del recipiente a presión. Es importante realizar una modelización precisa de la geometría, incluyendo detalles como las conexiones, soldaduras y refuerzos. Esto permitirá obtener resultados más precisos y representativos del comportamiento real del recipiente.
No considerar las condiciones de carga adecuadas:
Otro error común es no considerar las condiciones de carga adecuadas durante el análisis. Es importante tener en cuenta factores como la presión interna, la temperatura, las cargas externas y las condiciones de servicio a las que estará expuesto el recipiente. Estas condiciones deben ser definidas con precisión para obtener resultados confiables.
No realizar una correcta malla de elementos finitos:
La malla de elementos finitos es una parte fundamental del análisis de recipientes a presión con ANSYS. Un error común es no realizar una malla adecuada, lo que puede afectar la precisión de los resultados. Es importante garantizar una densidad adecuada de elementos en áreas críticas, como las zonas de concentración de tensiones o los puntos de conexión.
No considerar el material y las propiedades adecuadas:
Otro error común es no considerar el material y las propiedades adecuadas del recipiente durante el análisis. Es importante conocer las propiedades mecánicas del material, como la resistencia a la tracción, el módulo de elasticidad y la densidad. Además, es necesario considerar los efectos térmicos y las propiedades termomecánicas del material para obtener resultados precisos.
No validar los resultados obtenidos:
Finalmente, un error común es no validar los resultados obtenidos del análisis de recipientes a presión con ANSYS. La validación es un paso crucial para asegurar la precisión y confiabilidad de los resultados. Se pueden utilizar métodos de validación, como pruebas experimentales o comparación con resultados numéricos de casos similares, para asegurar que los resultados obtenidos sean consistentes.
Al realizar un análisis de recipientes a presión con ANSYS, es importante evitar errores comunes como no considerar la geometría real del recipiente, no considerar las condiciones de carga adecuadas, no realizar una correcta malla de elementos finitos, no considerar el material y las propiedades adecuadas, y no validar los resultados obtenidos. Evitar estos errores contribuirá a obtener resultados más precisos y confiables en el análisis de recipientes a presión.
Cuál es la importancia de la validación y verificación de los resultados en el análisis de recipientes a presión
La validación y verificación de los resultados en el análisis de recipientes a presión es de vital importancia para garantizar la seguridad y fiabilidad de estos equipos. Estos recipientes están diseñados para contener sustancias a presión, como gases y líquidos, y cualquier falla en su funcionamiento podría tener graves consecuencias.
En el análisis de recipientes a presión se utilizan herramientas como ANSYS, un software de simulación de ingeniería que permite modelar y analizar el comportamiento de estos recipientes frente a diferentes condiciones de carga. Sin embargo, es fundamental validar y verificar los resultados obtenidos a través de este software para asegurarse de que son precisos y confiables.
La validación implica comparar los resultados obtenidos a través de la simulación con datos experimentales o resultados analíticos conocidos. Esto permite evaluar la precisión del modelo y confirmar que el software está generando resultados coherentes. Por otro lado, la verificación implica asegurarse de que el software ha sido implementado correctamente y está generando resultados consistentes dentro de sus propias capacidades y limitaciones.
En el análisis de recipientes a presión, la validación y la verificación son esenciales para asegurar que los resultados obtenidos son confiables y pueden ser utilizados para tomar decisiones importantes en el diseño y la operación de estos equipos. Además, la validación y la verificación son requerimientos comunes en la industria y pueden ser necesarios para cumplir con regulaciones y estándares específicos.
La validación y verificación de los resultados en el análisis de recipientes a presión con ANSYS son fundamentales para garantizar la seguridad y fiabilidad de estos equipos. Estos procesos permiten evaluar la precisión del modelo y confirmar que el software está generando resultados consistentes. Además, son requerimientos comunes en la industria y pueden ser necesarios para cumplir con regulaciones y estándares específicos.
Cuáles son los beneficios y aplicaciones del análisis de recipientes a presión con ANSYS en diferentes industrias
El análisis de recipientes a presión con ANSYS es fundamental en varias industrias, ya que permite evaluar la capacidad de los recipientes para resistir las cargas internas y externas. Este tipo de análisis tiene numerosos beneficios y aplicaciones en diferentes sectores.
Uno de los principales beneficios del análisis de recipientes a presión con ANSYS es la capacidad para predecir y evitar fallos. Mediante la simulación numérica, es posible evaluar diferentes escenarios y determinar las tensiones y deformaciones críticas que podrían comprometer la integridad de los recipientes. De esta manera, las empresas pueden tomar medidas preventivas para garantizar la seguridad de sus operaciones.
Otro beneficio significativo es la optimización del diseño de los recipientes a presión. ANSYS permite realizar múltiples iteraciones y ajustes en el diseño con el fin de maximizar la eficiencia, reducir el peso y mejorar la durabilidad del recipiente. Esto se traduce en ahorros en costos de materiales y fabricación, así como en un rendimiento superior de los recipientes en servicio.
En cuanto a las aplicaciones, el análisis de recipientes a presión con ANSYS es ampliamente utilizado en la industria química y petroquímica. Estas industrias trabajan con fluidos altamente corrosivos y peligrosos, por lo que es crucial asegurarse de que los recipientes sean capaces de soportar las condiciones extremas y prevenir fugas o explosiones.
Además, el análisis de recipientes a presión es esencial en las plantas de energía, donde los recipientes juegan un papel fundamental en la generación y distribución de energía. La evaluación de la resistencia y estabilidad de estos recipientes es crucial para garantizar la seguridad y confiabilidad de los sistemas.
En el ámbito de la industria alimentaria y farmacéutica, el análisis de recipientes a presión con ANSYS también desempeña un papel importante. Aquí, es necesario asegurarse de que los recipientes cumplan con los estándares de calidad y que sean capaces de soportar las presiones requeridas para la producción y el almacenamiento de alimentos y medicamentos.
El análisis de recipientes a presión con ANSYS ofrece beneficios significativos en términos de seguridad y optimización de diseño. Además, tiene aplicaciones en diferentes industrias, desde la química y petroquímica hasta la energía, la alimentaria y la farmacéutica. Por lo tanto, es una herramienta esencial para garantizar la integridad y confiabilidad de los recipientes a presión en diversas aplicaciones industriales.
Existen estudios de caso o ejemplos reales de análisis de recipientes a presión con ANSYS que demuestren su eficacia y precisión
En la industria de la ingeniería y fabricación, el análisis de recipientes a presión es esencial para garantizar la seguridad y el rendimiento de los equipos. ANSYS es una herramienta de simulación líder que permite a los ingenieros llevar a cabo análisis detallados de recipientes a presión para evaluar su resistencia estructural y determinar las tensiones críticas.
Para demostrar la eficacia y precisión de ANSYS en el análisis de recipientes a presión, se han realizado numerosos estudios de caso y ejemplos reales. Estos casos de uso destacan cómo ANSYS puede simular diferentes tipos de recipientes a presión, desde cilindros hasta esferas y tanques de almacenamiento.
Por ejemplo, en un caso de estudio reciente, un fabricante de recipientes a presión utilizó ANSYS para simular el comportamiento de un tanque de almacenamiento a lo largo del tiempo. Mediante la modelización en 3D del tanque y sus conexiones, se evaluaron las tensiones y deformaciones bajo diferentes condiciones de carga y presión. Los resultados obtenidos con ANSYS permitieron al fabricante optimizar el diseño del tanque y garantizar su seguridad y durabilidad.
Otro ejemplo de análisis de recipientes a presión con ANSYS es el estudio de un cilindro sometido a presión interna y externa. Mediante la simulación en ANSYS, los ingenieros pudieron calcular las tensiones y deformaciones en diferentes puntos del cilindro, lo que les permitió determinar la vida útil del recipiente y tomar decisiones informadas sobre su mantenimiento y reemplazo.
Estos ejemplos demuestran claramente la eficacia y precisión de ANSYS en el análisis de recipientes a presión. La herramienta ofrece una amplia gama de funcionalidades, como la capacidad de modelar geometrías complejas, aplicar condiciones de carga realistas y simular diferentes materiales. Con ANSYS, los ingenieros pueden obtener resultados confiables y precisos para garantizar que los recipientes a presión cumplan con los estándares de seguridad y rendimiento más exigentes.
Preguntas frecuentes (FAQ)
1. ¿Qué es un recipiente a presión?
Un recipiente a presión es un contenedor diseñado para contener y almacenar fluidos a presiones superiores a la atmosférica. Son utilizados en diversas industrias como la química, petroquímica y alimentaria.
2. ¿Por qué es importante realizar un análisis de recipientes a presión?
Realizar un análisis de recipientes a presión es crucial para garantizar la seguridad y la integridad estructural del recipiente. Permite identificar posibles puntos de falla, evaluar la resistencia y la vida útil del recipiente, y cumple con los requisitos normativos y de seguridad.
3. ¿Cómo se realiza un análisis de recipientes a presión con ANSYS?
El análisis de recipientes a presión con ANSYS se realiza utilizando el módulo de análisis estructural de ANSYS. Se importa el modelo del recipiente, se definen las condiciones de carga y se aplican las propiedades del material. Luego, se realiza el análisis para evaluar la resistencia y la deformación del recipiente.
4. ¿Cuáles son los tipos de análisis que se pueden realizar con ANSYS?
Con ANSYS se pueden realizar diferentes tipos de análisis en recipientes a presión, como análisis estático lineal, análisis de fatiga, análisis de pandeo, análisis dinámico y análisis no lineal. Estos análisis permiten evaluar diferentes aspectos de la resistencia y el comportamiento del recipiente.
5. ¿Cuáles son los beneficios de utilizar ANSYS para el análisis de recipientes a presión?
ANSYS es una herramienta de simulación y análisis avanzada que ofrece numerosos beneficios para el análisis de recipientes a presión. Permite obtener resultados precisos y confiables, reduce los costos y el tiempo de desarrollo, y facilita el cumplimiento de los requisitos normativos y de seguridad.
Deja una respuesta
Entradas relacionadas